This past year was extremely busy with the development of a program to support the in-house design, manufacture, and operation of a Remotely Operated Vehicle. In 2015, the engineering team focused on the development of Schmidt Ocean Institute’s first 4,500 m underwater robotic vehicle, scheduled for delivery in 2016.
The engineering team successfully completed the vehicle’s final design, including reviews, in December, allowing for the components to be manufactured and put into production in early 2016.
In designing a vehicle specifically for Falkor, the over-boarding systems were specially designed to work with Falkor’s layout, capacity and power requirements. The major sub system components was also evaluated and subsequent vendors were selected based on performance and proven experience in similar ROV systems.
The engineering team worked closely with a selected Science Advisory Group (SAG) comprised of leaders in the field of marine exploration, marine robotics, and deep sea ecology. The SAG participated in a series of surveys designed to elicit their input on science mission requirements as well as the systems and equipment the deep ocean scientific user community would need to conduct research. The group’s input has been integral to the engineering team, allowing them to develop final specifications for the vehicle’s science systems including core sensors, lighting, cameras and navigation systems. The imaging system specifications and final designs will include state-of-the-art science cameras, capable of transmitting both 4K Ultra High Definition (UHD) video and 20 megapixel still images from the same camera.
Additionally, the electrical engineers on the ROV team have worked closely with an external vendor to develop a collaborative, custom-designed, subsea electronics and telemetry system. This system will be housed in two same sized pressure housings supported by a state-of-the-art technologically innovative user interface, which is commencing final manufacture.
With most of the primary components and sub systems specified, a final vehicle layout was determined. The resulting information from the weights and balance was used to finalize the designs of the syntactic foam and main vehicle frame. The design is nearing completion with the final manufacturing details being worked out with the frame fabricators to ensure the plans support successful manufacturability. The team is looking forward to integration of all the vehicle subsystems, followed by tank testing and sea trials in Guam later in 2016.
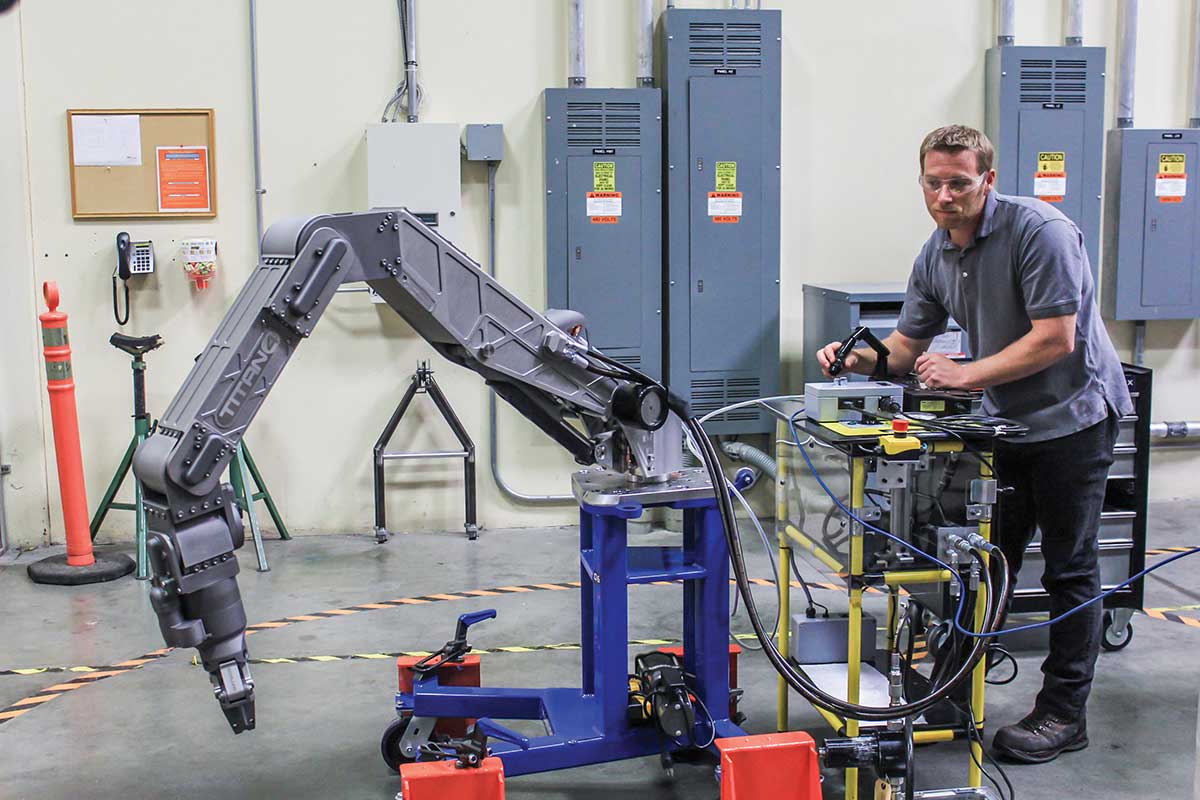